Von der Antike bis heute ist die Gießerei ein unverzichtbarer Eckpfeiler der Produktion und prägt mit ihrer vielfältigen Produktpalette die Welt um uns herum. In unserer Gießerei setzen wir fortschrittliche und effiziente Verfahren ein, um die Herstellung qualitativ hochwertiger Gussteile zu gewährleisten.
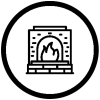
Der Schmelzprozess wird mit zwei EGES-Mittelfrequenz-Induktionsöfen mit einer Kapazität von 2×6 Tonnen durchgeführt. Diese Öfen sind mit einem modernen System zur Erfassung von Feststoffemissionen von BMD GARANT ausgestattet. Dieses System gewährleistet Umweltverträglichkeit und Sicherheit. Die elektrischen Mittelfrequenz-Induktionsschmelzöfen INDUCTOTHERM ELPHIAC mit einer Kapazität von 2×5 Tonnen dienen als Reserve-Schmelzanlage.
Grauguss
Wir sind spezialisiert auf die Herstellung von Grauguss in den Sorten ČSN 42 2415 bis ČSN 42 2425 (entspricht EN-GJL-150 (GG 15) bis EN-GJL-250 (GG 25)).
Gusseisen
Das Gusseisen wird in der Qualität ČSN 42 23 05 (entspricht EN-GJS-500-7 (GGG 50)) hergestellt.
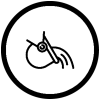
Wir zeichnen uns durch das Gießen einer breiten Palette von Gewichten von 2 kg bis 100 kg in sorgfältig gefertigte Formen aus synthetischen Bentonitverbindungen aus. Unsere beiden automatischen Formanlagen sind mit Formmaschinen der renommierten deutschen Firma Heinrich Wagner Sinto ausgestattet. Diese Anlagen arbeiten nach dem Prinzip, dass die Formmasse mit der Formanlage in den Rahmen gegossen, die Form mit Druckluft aufgeblasen und dann unter Druck gesetzt wird. Beide Anlagen bieten auch die Möglichkeit, während des Prozesses Kerne in die Formen einzulegen, was die Komplexität und Kompliziertheit der Gussteile erhöht.
HSP 3D-Rahmen-Formanlage
Eine unserer neuesten Technologien ist die HSP3D-2-Anlage, die seit Januar 2023 in Betrieb ist. Diese hochmoderne automatische Anlage verfügt über eine geteilte Formplatte und bietet eine beeindruckende Leistung von 60 kompletten Formen pro Stunde. Die Abmessungen des Formrahmens betragen 850 x 850 x 200/200 mm und ermöglichen es uns, verschiedene Gussanforderungen mit unübertroffener Präzision zu erfüllen.
Halbform-Erhöhung bis zu 50 mm
Die erste Generation der HSP3D-1-Formanlage ist seit 2002 in Betrieb. Die Größe des Formrahmens beträgt 850 x 850 x 200/200 mm, mit der Möglichkeit, die Halbform bei Bedarf um 50 mm zu vergrößern. Diese Anlage hat eine Kapazität von 50 kompletten Formen pro Stunde, was unsere Produktionskapazitäten weiter erhöht und den Anforderungen verschiedener Projekte entspricht.
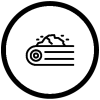
Unser Formmischungsprozess ist ein Beweis für Modernität und Effizienz. Das Herzstück dieses Prozesses ist eine Mischanlage, die mit einem modernen Turbinenmischer MTI 2500 von TECHNICAL ausgestattet ist. Um eine präzise Wasserdosierung zu gewährleisten, setzen wir ein automatisiertes System von MICHENFELDER ein, das die Genauigkeit unserer Sandmischungen garantiert. Die Formmasse wird luftgekühlt und bei Bedarf mit Wasser in Form eines Wasser-Aerosols nachgekühlt. Das Besondere an unserer Formmischung ist der vollautomatische Prozess, der menschliche Eingriffe überflüssig macht und die Produktionseffizienz bei gleichbleibender Qualität maximiert.
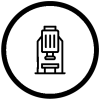
Für die Kernherstellung verwenden wir die LAEMPE LL20-Maschine, die ein Kerninjektionsvolumen von bis zu 30 Litern bietet, ergänzt durch eine Amingasaushärtung für außergewöhnliche Kernintegrität. Außerdem setzen wir die RÖPER 40 Maschine ein, die für ihr beeindruckendes Kerninjektionsvolumen von bis zu 40 Litern und den ebenso zuverlässigen Amingas-Härtungsprozess bekannt ist.
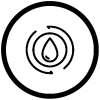
Der Haupttransport der Gussteile von den Formanlagen zur Verzinnungsanlage erfolgt über einen langsam laufenden Magaldi-Gliederbandförderer, gefolgt von einem effizienten Vibrationsrinnenförderer, der als logistisches Bindeglied zwischen den Stationen dient. Für eine einfache Handhabung verfügen unsere engagierten Mitarbeiter über einen hydraulischen Manipulator von CLANSMAN DYNAMICS, um den Handhabungsprozess zu rationalisieren und einen reibungslosen Ablauf zu gewährleisten.
Wir vergessen auch nicht die Abkühlung der Gussteile, für die wir ihnen in unserer Kühlhalle ausreichend Zeit geben (Kühlzeit bis zu 24 Stunden). Nach der Kühlphase werden die Gussteile in der Strahlanlage sorgfältig bearbeitet. Hier werden alle Rückstände der Formmasse präzise entfernt, um ein perfektes Oberflächenfinish zu erzielen. Die moderne KONRAD RUMP-Strahlanlage mit einer beeindruckenden Strahlmittelmenge von 300 kg/min sorgt dafür, dass jedes Gussteil perfekt gereinigt und für die weitere Bearbeitung vorbereitet ist. Darüber hinaus ist die Anlage mit einer Filteranlage ausgestattet, die einen sauberen und umweltfreundlichen Prozess gewährleistet.
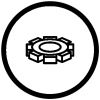
Je nach Kundenwunsch führen wir verschiedene Oberflächenbehandlungen durch. Farbvarianten in synthetischen rotbraunen oder schwarzen Grundtönen. Wir bemühen uns, verschiedene Bedürfnisse zu erfüllen, z.B. Komaxitierung in verschiedenen Farbtönen oder Feuerverzinkung. Wir bieten auch die Gussbearbeitung (Drehen, Fräsen, Bohren usw.) an, sowohl auf konventionellen als auch auf NC- und CNC-Maschinen.